فرایند فرم دهی به روش اکستروژن EXTRUSION
فرایند فرم دهی به روش اکستروژن EXTRUSION یکی از رایج ترین فرایندهای فرم دهی در دنیای تولید امروز است. اکستروژن Extrusion process شامل استفاده از انواع زیادی از مواد مانند فلزات، پلاستیک، سرامیک، و غیره است که برای فرم دهی و دستیابی به خواص بهتر آنها استفاده میشود. فرایند Extrusion در فلزات ممکن است استحکام مواد را افزایش دهد.
عملکرد اصلی این فرایند این است که مواد شکننده را به راحتی به محصول مورد نظر تبدیل میکند. میتوان ادعا کرد که اکستروژن یک فرایند نیمه پیوسته یا حتی پیوسته است که برای تشکیل مواد گرم یا حتی سرد استفاده میشود.
اکستروژن یا روزنرانی (Extrusion) چیست؟
Extrusion اکستروژن یک فرایند قالب گیری تولیدی است که شامل یک قالب پیششکل برای ایجاد اجسام با شکل و مشخصات خاص است. این فرایند برای ایجاد اشیا با مشخصات مقطع ثابت استفاده میشود. در هنگام کار، مواد از طریق یک قالب با سطح مقطع مورد نظر رانده میشوند، شکل آن ها تغییر میکند تا شکل قالب را منعکس کنند. محصولات Extrusion به طور کلی «اکسترودات» نامیده میشوند.
نسبت اکستروژن:
نسبت اکستروژن عبارت است از سطح مقطع آغاز تقسیم بر سطح مقطع Extrusion نهایی. یکی از مزایای فرایند اکستروژن این است که این نسبت میتواند بسیار زیاد باشد؛ در حالی که همچنان قطعات با کیفیت بالا تولید میشود. این فرایند توانایی ایجاد مقاطع بسیار پیچیده و کار با مواد شکننده را دارد زیرا این ماده تنها با تنشهای فشاری و برشی مواجه است.
فرایند Extrusion همچنین سطح عالی را به قطعات میبخشد و آزادی قابل توجهی برای اشکال مختلف در فرایند طراحی میدهد.
فرایندهای اکستروژن شبیه به کشش است که از استحکام کششی ماده برای کشیدن آن از درون قالب استفاده میکند. فرایند کشش برای تولید سیم، میله فلزی و لوله استفاده میشود.
با این حال، به اشکال ساده تر محدود میگردد و بر خلاف Extrusion که همه را در یک مرحله انجام میدهد، معمولا چندین مرحله مورد نیاز است.
اکستروژن به صورت پیوسته (از لحاظ نظری تولید مواد طولانی مدت نامحدود) یا نیمه پیوسته (تولید قطعات زیادی) شناخته شده است. مواد متداول مورد استفاده در فرایند Extrusion یا روزنرانی فلزات، پلیمرها، سرامیکها، بتن، خاک رس مدل سازی و مواد غذایی هستند.
محصولات فرآیند اکستروژن:
در زندگی روزمره محصولات فرآیند اکستروژن بسیار فراوانی دارند. از ساده ترین محصولات مانند تیوب خمیر دندان تا پیچیده ترین مانند پروفیلهای آلومینیومی و … طیف عظیمی از تولیدات و کاربردهای فرآیند اکستروژن میباشد که نشان از انعطاف پذیری بسیار زیاد این روش است.
در ذیل برخی از کالاها که در ساخت آنها از اکستروژن استفاده شده را شرح میدهیم:
- تولید لوله و پروفیل (Profile & pipe production)
- تولید دانه گرانول (Granule production)
- تولید ورقههای بسیار نازک به طریقه بادی (Film blowing)
- قالبگیری بادی (Blow Molding)
از فرآیند اکستروژن در تولید انواع محصولات پلاستیکی و انواع جدارهها مانند لوله(پلی اتیلن X3)، میله تو پر ، ورق ، روکش سیم، تولید نایلون و نایلکس(پلی اتیلن F7000) بسته بندی، کیسههای خرید و تبلیغاتی، کیسههای سرم، بسته بندی معمولی و مخصوص مواد غذائی (با لایۀ ضد نفوذ اکسیژن)، پوشش گلخانهها و سفرههای یکبار استفاده میکنیم.
فرایند تولید به روش اکستروژن (Extrusion):
اکستروژن را میتوان به طور کلی به دو نوع طبقه بندی کرد: یکی اکستروژن گرم و دیگری اکستروژن سرد. این دسته بندیهای فوق نیز به دستههایی تقسیم میشوند.
فرایندهای اکستروژن گرم با حرارت دادن مواد موجود آغاز میشود که سپس در ظرف پرس بارگذاری میشود. یک بلوک ساختگی در پشت آن قرار داده شده است که در آن یک گوچ مواد را فشار میدهد تا آن را از قالب خارج کند.
سپس اکستروژن کشیده میشود تا صاف شود. قطعه در صورت نیاز به یک ویژگی خاص یا بهتر تحت عملیات تکمیلی سردکار یا حرارتی قرار میگیرد.
فرایند اکستروژن EXTRUSION گرم: 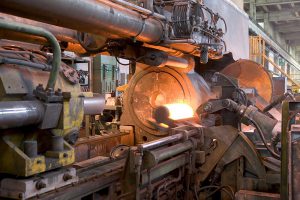
این یک فرایند کار گرم است، یعنی بالاتر از دمای تبلور مجدد مواد انجام میشود. این کار از سخت شدن مواد جلوگیری میکند و باعث میشود که مواد از مجراهای قالب راحتتر عبور کنند.
فرایند اکستروژن گرم بیشتر بر روی پرسهای هیدرولیک افقی انجام میشود که از 230 تا 11000 تن متریک (250 تا 12130 تن کوتاه) متغیر است. فشار آن ها از 30 تا 700 مگاپاسکال (4400 تا 101500 psi) متغیر است.
بنابراین، روغن کاری مورد نیاز است. روغن یا گرافیت برای اکستروژن با دمای پایین تر استفاده میشود، در حالی که پودر شیشه برای اکستروژن با دمای بالاتر به کار میرود.
مواد فلزی در اکستروژن گرم به دماهای متفاوتی نیاز دارند. موادی مانند منیزیم، آلومینیوم، مس، فولاد، تیتانیوم، نیکل، آلیاژ نسوز و غیره همه اینها در طول فرایند روزنرانی گرم به دماهای متفاوتی نیاز دارند. این فرایند معمولا برای دستیابی به تعادل مناسب نیروهای مورد نیاز، شکل پذیری و خواص روزنرانی نهایی استفاده میشود.
فرآیند اکستروژن سرد: 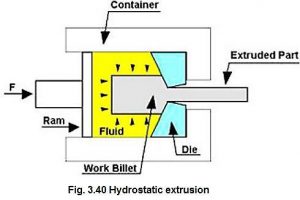
انجام فرایندهای اکستروژن سرد در دمای اتاق یا نزدیک به دمای اتاق صورت میپذیرد. از مزایای آن نسبت به فرایند گرم میتوان به عدم اکسیداسیون، استحکام بالاتر به دلیل کار سرد، تلرانس نزدیکتر، پرداخت سطح بهتر و سرعت اکستروژن سریع اشاره کرد.
موادی که معمولا در فرایندهای روزنرانی سرد استفاده میشوند عبارتند از: سرب، قلع، آلومینیوم، مس، زیرکونیوم، تیتانیوم، مولیبدن، بریلیم، وانادیم، نیوبیوم و فولاد. کاربردهای فرایند اکستروژن سرد شامل لولههای جمع شونده، کیسهای خاموش کننده آتش نشانی، سیلندرهای کمک فنر و جعبه دنده است.
انواع روشهای فرآیند اکستروژن با توجه به جهت جریان مواد:
اکستروژن مستقیم Direct Extrusion:
این نوع فرایندهای Extrusion به مواد اجازه میدهد تا در جهت تغذیه پانچ جریان پیدا کنند. این پانچ در طول فرایند به سمت قالب حرکت میکند.
اکستروژن مستقیم به دلیل اصطکاک بیشتر بین بیلت و ظرف به نیروی بیشتری نیاز دارد. Extrusionمستقیم که به عنوان روزنرانی حمل و نقل نیز شناخته میشود، در دنیای صنعتی بسیار رایج است.
شمش در کار خود در یک ظرف با دیواره سنگین قرار میگیرد که توسط گوچ یا پیچ از داخل قالب عبور میکند. یک بلوک ساختگی قابل استفاده مجدد بین گوچ و شمش به جدا نگه داشتن آن ها کمک میکند.
محدودیت اصلی استفاده از این فرایند این است که نیروی مورد نیاز برای اکسترود کردن بیلت زیاد است. این به دلیل نیروهای اصطکاک ایجاد شده توسط نیاز به حرکت بیلت در تمام طول ظرف است. با توجه به نیروی بیشتر مورد نیاز در ابتدای فرایند و به آرامی با مصرف بیلت کاهش مییابد. قبل از پایان شمش، نیرو به شدت افزایش مییابد زیرا شمش یک ماده است و ماده باید به صورت شعاعی جریان یابد تا از قالب خارج شود.
اکستروژن غیر مستقیم Indirect Extrusion: 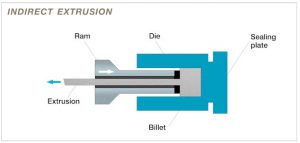
در یک فرایند Extrusion غیرمستقیم، مواد کار به سمت خلاف جهت حرکت پیستون جریان مییابند. قالب در سمت مخالف حرکت پانچ نصب میشود. این ماده از فضای حلقوی بین پانچ و ظرف عبور میکند.
همچنین به عنوان روزنرانی عقب شناخته میشود. در این فرایند خود شمش و ظرف در حالی که قالب ثابت است با هم حرکت میکنند.
یک «ساقه» بلندتر از طول ظرف به نگه داشتن قالب کمک میکند. حداکثر طول اکستروژن در نهایت با استحکام ستون ساقه مشخص میشود. حرکت بیلت با ظرف، نیروهای اصطکاکی را که ممکن است ایجاد شود از بین میبرد.
مزایای اکستروژن غیر مستقیم:
- در این روش 25 تا 30 درصد اصطکاک کاهش مییابد. این اجازه میدهد تا بیلتهای بزرگتر اکسترود شوند و میتوان آن را با سرعت بیشتری انجام داد.
- آستر ظرف ماندگاری بیشتری دارد. زیرا کمتر دچار سایش میشود.
- بیلت به طور یکنواختتر استفاده میشود و در نتیجه عیوب کمتر و دانه درشتی ایجاد میشود.
معایب اکستروژن غیر مستقیم:
- عیوب و ناخالصیهای سطح بیلت بر سطح Extrusion تاثیر میگذارد.
- به دلیل سطح مقطع محدود، این فرایند به اندازه Extrusion مستقیم چند منظوره نیست.
اکستروژن هیدرواستاتیک Hydrostatic Extrusions: 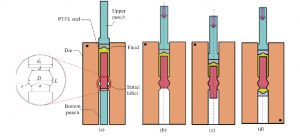
در این نوع Extrusion از سیال برای اعمال فشار بر روی بیلت استفاده میکنند. در این فرایند اصطکاک از بین میرود زیرا شمش با دیواره سیلندر یا پیستون در تماس نیست. سیالی بین بیلت و پیستون وجود دارد و پیستون نیرویی را به سیال وارد میکند که بیشتر بر روی بیلت اعمال میشود.
روغنهای گیاهی معمولا به عنوان سیال در اکستروژن هیدرواستاتیک استفاده میشوند. یکی از اثرات این فرایند مشکل نشتی و سرعت کنترل نشده است این فرایند را میتوان گرم یا سرد انجام داد، اما دما به دلیل پایداری سیال مورد استفاده محدود میشود. برای انجام این فرایند باید از یک سیلندر آب بند شده حاوی محیط هیدرواستاتیک استفاده شود.
امکان تحت فشار قرار دادن سیال از دو طریق وجود دارد. در مرحله اول، Extrusion با سرعت ثابت، یعنی یک قوچ یا پیستون برای تحت فشار قرار دادن سیال داخل ظرف استفاده میشود.
در مرحله دوم، اکستروژن با فشار ثابت – از یک پمپ و احتمالا با یک تقویت کننده فشار، برای تحت فشار قرار دادن سیال استفاده میشود. سپس به قالب پمپ میشود.
مزایای اکستروژن هیدرواستاتیک:
- به دلیل عدم اصطکاک بین ظرف و شمش، نیاز به نیرو کاهش مییابد.
- سرعتهای بالاتر، نسبتهای کاهش بیشتر و دمای پایینتر بیلت
- شکل پذیری مواد با اعمال فشار زیاد افزایش مییابد.
- باقیمانده بیلت روی دیواره قالب برجای نمیماند.
- هم بیلت های بزرگ و هم مقاطع بزرگ را میتوان اکسترود کرد.
معایب اکستروژن هیدرواستاتیک:
- بیلتها باید با باریک کردن یک سر آماده شوند تا با زاویه ورودی قالب مطابقت داشته باشند. یعنی باید یک مهر در ابتدای دایره شکل بگیرد.
- برای رفع هر نوع مشکل و نقص سطحی لازم است که همه بیلت ماشین کاری شود.
- یافتن سیالی که فشارات فوق العاده بالای مورد نیاز را تحمل کند میتواند دشوار باشد.
- برای جلوگیری از آزاد شدن ناگهانی سیال اکستروژن، باید بقایای بیلت یا یک پلاک از مواد سخت تر در انتهای Extrusion باقی بماند.
مشکلات رایج اکستروژن EXTRUSION عبارتند از:
- نقصهای زیبایی شناختی (به عنوان مثال، گودالها، مشخصات سیاه، سوراخهای سوزنی، علائم کشیدن، خطوط قالب، علائم سینک)
- واریانس اندازه (که میتواند متناوب یا پیوسته باشد)
- تغییرات ابعادی
- سطح ناهموار به دلیل ذرات ذوب نشده
- اکسترود سوخته و تغییر رنگ داده
- شکستگی مذاب
- حباب در سطح نمایه
- بدون خروجی: قالب به دلیل انجماد مسدود شده است.
- موج: به دلیل مواد آلوده، تنظیمات دمایی اشتباه، یا خروجی نامتعادل قالب رخ میدهد.
مزایای فرآیند اکسترود:
در زیر مزایای فرایند اکستروژن در کاربردهای مختلف آن ها آورده شده است:
- خواص مکانیکی بالا را میتوان با اکستروژن سرد به دست آورد.
- یک مقطع پیچیده را میتوان به راحتی ایجاد کرد.
- میتوان روی مواد شکننده و انعطاف پذیر کار کرد.
- نسبت اکستروژن بالا
- هزینه کم برای هر قطعه
- انعطاف پذیری عملیات
- در اکستروژن داغ، تغییرات پس از اجرا آسان است. زیرا محصول هنوز در شرایط گرم است
- عملکرد متوالی
- حجم تولید بالا
- تنوع مواد اولیه برای استفاده زیاد است.
- اختلاط یا ترکیب خوب
- سطح به دست آمده خوب است.
- خواص مکانیکی خوب به دست آمده در اکستروژن سرد
معایب فرآیند اکستروژن EXTRUSION:
علی رغم مزایای خوب فرایند Extrusion، برخی محدودیت ها هنوز وجود دارد. در زیر معایب فرایند اکستروژن در کاربردهای مختلف آن ها آورده شده است:
- هزینه اولیه یا راه اندازی بالا
- نیاز به نیروی فشاری بالا
- تنوع در اندازه محصول
- محدودیت های محصول به دلیل تنها یک نوع سطح مقطع را میتوان در یک زمان به دست آورد.
اکستروژن و صنعت پلاستیک :
پلاستیک یکی دیگر از مواد رایج مورد استفاده برای اکستروژن EXTRUSION است. آنها معمولا به عنوان تراشههای پلاستیکی یا گلولهها استفاده میشوند که برای حذف رطوبت از آنها خشک میشوند.
در تجهیزات اکستروژن، مواد از طریق یک قیف تغذیه میشود، که سپس با ترکیبی از عناصر گرمایش و حرارت برشی از پیچ Extrusionبه حالت مذاب گرم میشود. پیچ، یا زمانی که Extrusion دو پیچی آن پیچ میشود، رزین را از طریق قالب وارد میکند و به رزین شکل دلخواه میدهد.
برای تهیه مواد اولیه پلاستیک که قابلیت فرم دهی به روش اکستروژن را دارند با کارشناسان ما در پانیذا پلیمر تماس حاصل فرمایید.
دیدگاهتان را بنویسید